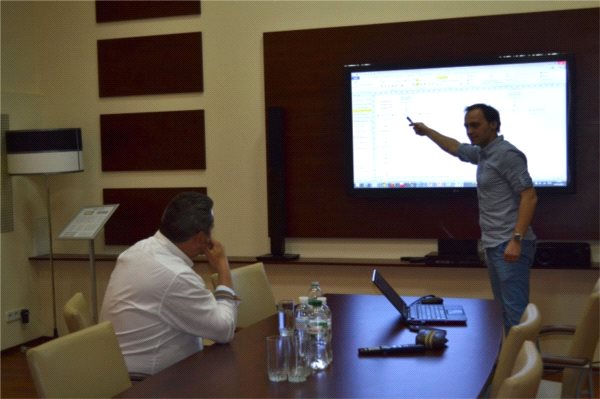
Znaczenie analizy procesów przy podjęciu decyzji o ich mechanizacji
Wsparcie decyzji o automatyzacji procesów logistycznych poprzedzona analizą przepływów istniejących lub planowanych jest typową ścieżką decyzyjną przygotowującą inwestycje w magazynie. Metoda mapowania procesów i jej przygotowanie wieloetapowe jak przykład prawidłowej oceny...
W artykule postaram się przedstawić metodykę mapowania, czyli konieczność oceny procesów według założeń metody mapowania oraz jakie elementy musi zawierać każda mapa procesu
Podjęcie decyzji o automatyzacji procesów magazynowych
Najczęściej decyzja o automatyzacji w magazynie wyzwala się z potrzeby chwili i ma swoje podłoża w braku efektywności i chęci jej zwiększenia, braku dostępności zasobów ludzkich lub koniecznością zaspokojenia potrzeb klientów w coraz krótszym czasie. Prowadząc rozmowy z klientami, którzy zaleźli się w opisanej sytuacji bardzo często pojawia się priorytet szybkiej realizacji pomysłu w oparciu o bardzo konkretną technologię, podpatrzoną w innym zakładzie, na targach lub w Internecie. Takie bezrefleksyjne podejście do tematu ma zwyczajowo zakończenie w postaci nieudanej inwestycji, rozczarowaniu (do dostawcy, własnego zespołu, doradcy) lub frustracji w przypadku, gdy konkurencyjnemu zakładowi taka inwestycja przyniosła wymierne korzyści.
Przystępując do współpracy z naszymi klientami oferujemy na wstępie audyt procesów logistycznych, tak aby zapoznać się ze specyfiką ich działalności, metodami przechowywania, kompletacji i wysyłki ich towarów, oraz z potrzebami klientów końcowych. Na podstawie obserwacji przepływów towarowych w magazynie klienta i poczynionym obserwacjom przystępujemy do pierwszej fazy projektu – MASTER PLANOWANIA.
MASTER PLANNING
Proces MASTER PLANOWANIA rozpoczyna się od identyfikacji podstawowych wielkości logistycznych przepływów zarówno od strony ilościowej jak i jakościowej (struktur zadaniowych lub zleceń realizowanych w następujących po sobie procesach).
Wyniki analiz statystycznych (statycznych z punktu widzenia osi czasowej dla węzła procesowego) lub przepływowych (dynamicznych przy określeniu natężenia przepływu od punktu do punktu procesu) stają się podstawą do analizy i mapowania przyszłych procesów.
W wyniku wstępnego planowania procesów (high level) powstaje ich definicja operacyjna, czyli opis założonych czynności lub przebieg strumienia towarowego. W definicji procesów stosujemy również metodykę określającą jakie parametry są/będą zmiennymi i jakich efektów (wyników działania procesu) oczekujemy). Takie postępowanie jest pierwszym krokiem przybliżenia w całym łańcuchu działania polegającego na mapowaniu, ale daje możliwość bez „zagubienia” się w nadmiernej ilości detali, przygotowania opracowania będącego przygotowaniem do dalszego etapu – mapowanie procesów.
Pewną praktyczną pomocą na tym etapie jest również nakreślenie położenia danych procesów w całości przestrzeni magazynowej z oznaczeniem, kto i gdzie jaką rolę przy tym odgrywa, oraz wstępna definicja kierunków przepływu np. za pomocą wskazówek strumieniowych, ścieżek procesu i potrzebnych nośników strumienia (palety, skrzynie itd.).
Absolutnie koniecznym jest jednak na tym wstępnym etapie ścisła definicja celu danego procesu. Bez tej wydawałoby się oczywistej kwestii, nie można przystąpić do rzetelnej oceny danego procesu z punktu widzenia jego celowości, wydajności, pozycji w całym łańcuchu procesów, czy też wreszcie dokonać jego oceny ekonomicznej przydatności w całokształcie naszej pracy nad strumieniem towarowym.
Mapowanie Procesów
Mapowanie jest procesem opisywanym przez wielu autorów w wielu pozycjach naukowych czy opracowaniach praktycznych. Definicje te różnią się w zależności od punktu widzenia przydatności przeprowadzania samego mapowania, ale jeden element jest wspólny dal wszystkich – struktura czy też charakterystyka procesu mapowania. Każda definicja procesu musi zawierać następujące elementy:
- początek i koniec procesu
- strukturę procesu
- wejścia i wyjścia do procesu lub jego składowych
- definicję aktorów biorących udział w procesie (dostawcy, pracownicy itd.)
- kto jest właścicielem procesu w sensie wykorzystania jego rezultatu lub odpowiada za jego nadzór
- kryteria oceny efektywności (w praktyce stosuje się wiele wskaźników oceny efektywności procesu, niemniej zalecamy ich ograniczenie do nie więcej jak cztery, gdyż w przeciwnym razie grozi wzajemne wykluczanie się wskaźników i do blokady samego procesu)
- wpływ na całość łańcucha procesowego – to może być np. wskaźnik przydatności do wypracowania efektu końcowego tzw. wskaźnik udziału w sukcesie
- narzędzia służące do pomiaru
- kryteria i narzędzia służące do sterowania procesem
- zasoby (ludzkie, materialne, IT itd.) służące realizacji procesu a jednocześnie mające wpływ na jego koszty
- scenariusze odstępstw od zasadniczego procesu
- dokumentacja procesu.
Wymienione powyżej elementy mają tworzyć szkielet każdego z kreowanych przez nas procesów, a jednocześnie pozwolić nam na systematyczne i uporządkowane prowadzenia ich korekt, zmian logicznych, czy też analiz wartościowych.
Praca nad mapowaniem procesów i optymalizacja
W stworzonym przez nas obrazie działalności operacyjnej zakładu produkcyjnego lub magazynu logistycznego, będziemy się poruszać po „ścieżkach” (path lub stream to pojęcia wprowadzone w naszej działalności operacyjnej i analitycznej w szeregu prowadzonych przez nas projektów, lepiej oddających znaczenie, tego co staramy się odzwierciedlić narzędziem mapowania np. za pomocą wykresów Sankey’a) dokonując codziennych analiz bieżących lub poszukując potencjału do optymalizacji czasu i kosztów.
Przykładem analizy opartej na mapowaniu procesów jest poszukiwanie tzw. „wąskich gardeł” i zakłóceń w procesach mających wpływ na ich całkowitą efektywność. W tym przypadku schematy algorytmiczne procesu połączone ze strukturą danych o przepływach pozwala na symulowanie przeciążeń w procesie mogących doprowadzić do jego zatrzymania lub przekroczenia progu jego efektywności (poszukiwania optymalizacyjne np. za pomocą urządzeń mechanicznych).
W połączeniu z poszukiwaniem wartości strumienia można wyciągnąć wnioski o wartości zwrotu z inwestycji (Return Of Investment) lub przydatności danego procesu we własnych strukturach (decyzje typu „make or buy”). W ten sposób prowadzimy definicję posiadanych zasobów w dziale logistyki lub w produkcji, określając jednocześnie ich zapotrzebowanie na przyszłość lub w okresach spiętrzeń.
W tym obszarze działania zalecam jednak daleko idącą ostrożność w interpretacji wyników. Dla mało wprawnego oka, wyniki analiz cząstkowych procesów mogą prowadzić do mylnych wniosków np. polegających na zaspokojeniu potrzeb zasobowych zbyt dużym zapasem towarów i komponentów lub zasobów ludzkich wyrażonych w FTE. Doradzam naszym klientom podczas takich analiz ciągłe porównywanie wyników zmian przeprowadzonych dla jednego odcinka procesowego na całość łańcucha procesów i potrzeb. Możliwe jest mianowicie „przepełnienie” procesu zasobami (np. w wyniku zaokrągleń, co przy istnieniu dużych strumieni prowadzi do odpowiednio dużych tolerancji i odchyleń), co w konsekwencji prowadzi do utraty efektywności w rachunku całkowitym.
Z drugiej strony wprowadzanie współczynników korekcji lub ograniczania wartościami progowymi, skieruje nas na „łatwą ścieżkę” oszczędności, tylko po to aby obronić własną teorią.
Budując mapę procesów, pamiętajmy również o budowaniu ich podprocesów (jeżeli takie istnieją) i porównywaniu ich efektywności ekonomicznej, gdyż samo tworzenie mapy procesów nie może być celem samym w sobie.
Celem pośrednim (lub głównym w zależności od celu samego mapowania) może być stworzenie przy okazji mapowania procesów, również mapowanie kompetencji. To zestaw zależności pomiędzy zasobami, z których wynika z jednej strony rola w procesie, z drugiej zaś ich wpływ na jakość lub przepustowość procesu. I nie chodzi to o wartościowanie tymi samymi wskaźnikami, co strumienie przepływu, a o ustalenie źródła pochodzenia wartości dodanej do produktu lub strumienia i kierowanie tych kompetencji na obszary nadrzędne lub pokrewne w celu wypracowania większej wartości końcowej produktu lub strumienia.
Pośrednio w ten sposób zmapowane procesy, tworzą siatkę struktury organizacyjnej i co za tym idzie siatki odpowiedzialności za jakość i zdolność wytwórczą procesu. W oparciu o taką strukturę tworzymy kolejno sieć powiązań informatycznych, procedury i instrukcje procesowe pozwalające następnie na ich walidację lub kontrolę jakości.
Niemniej ważnym aspektem mapowania procesowego jest ciągły pomiar ich efektywności. Opisana już wyżej ilość wskaźników pomiaru połączona np. za pomocą strukturyzowanej i ujednoliconej karty wyników (Balanced Score Card) daje z jednej strony możliwość prowadzenia bieżącego nadzoru nad efektywnością, z drugiej zaś umożliwia na efektywną re-inżynierię procesów w poszukiwaniu udoskonaleń procesowych prowadzących do ich zawężenia (Lean Management).
Ryzyko towarzyszące metodzie mapowania
Będąc zwolennikiem jasnej i przejrzystej struktury wszystkich procesów, mam jednak świadomość słabych stron metody mapowania, na które chciałbym zwrócić uwagę czytelników.
Tworząc strukturę procesów np. pomiędzy dwoma gniazdami produkcyjnymi elementu wykonywanego przez zakład produkcyjny wielkoseryjny, tworzymy jednocześnie podwaliny dla utrwalenia jego jakości jak również dla polepszenia efektów ekonomicznych będących wynikiem naszego działania w tym procesie.
W dystrybucji towarów wrażliwych, niebezpiecznych lub farmaceutycznych, ścisłe zachowanie opracowanych procedur według przygotowanych uprzednio map procesowych jest koniecznością np. podczas ich walidacji. Niemniej i tutaj mogą wystąpić zjawiska powodujące naruszenie procedur. Są one jednak najczęściej spowodowane czynnikami zewnętrznymi jak np. brakiem odpowiedniego przygotowania lub brakiem czasu na dopasowanie tychże procedur w oprogramowaniu WMS. W ten sposób tworzą się dwa światy równoległe: mapowanych i zapisanych w oprogramowaniu procesów.
Jaki wpływ ma mapowanie na procesy w logistyce np. internetowej sprzedaży?
Wszędzie tam, gdzie zmiany procesowe towarzyszą nam na stałe w naszej pracy (ze względu na zmieniający się asortyment produktów lub ze względu na zmieniające się zachowania klientów, a co za tym idzie konieczność dopasowania procesu do tych zachowań), będziemy poruszali się w siatce struktur, która może okazać się zbyt sztywna i nie wytrzyma ona konfrontacji z codziennością, gdzie celem nadrzędnym jest elastyczność. Kolejne przeprowadzane przez nas korekty mapy procesowej doprowadzą mimowolnie do „znużenia” wykonywaniem pracy dla pracy i może okazać się szybko iż nie nadążamy za zmianami codziennych operacji.
Również fluktuacja załogi w magazynie, będzie naszym naturalnym wrogiem, mimo iż to właśnie uporządkowane procesy powinny ułatwić przygotowanie kolejnych zespołów.
W tej sytuacji zalecamy naszym klientom obranie ścieżki będącej rodzajem „mapy drogowej głównej”, tj. mapowania i opisywania procesów na poziomie nadrzędnym, tak aby procesy wykonawcze I-rzędu nie stały z nimi w sprzeczności, a jednak dawały możliwość operacyjnych dostosowań.
Takim przykładem jest opisanie stanowiska przygotowania do wysyłki i pakowania. Przygotujmy dla nich opis procesu polegający na definicji i trybie postępowania w przypadku zleceń jedno- lub wieloelementowych (SINGLE- / MULTI-PIECES ORDER), sposób ich dzielenia na stanowiska pracy, oraz sposób sortowania, ale już to czy temu towarzyszą dokumenty lub czy też klienci typu VIP uzyskają dodatkowe prezenty zamieśćmy w indywidualnej instrukcji roboczej stanowiska. I nie ma w tym sprzeczności, a jedynie poziom opisanych i mapowanych procesów jest o rząd wyższy, pozostawiając pewną swobodę operacyjną.