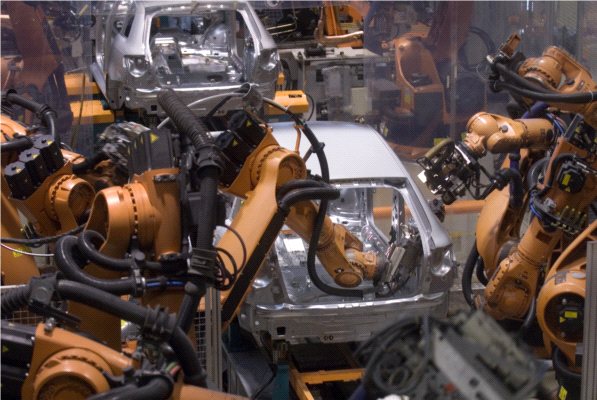
Wysoka zmienność produkcji
Współczesne realia rynkowe ukazują rosnącą potrzebę klientów dotyczącą możliwości wybierania spośród coraz to bardziej zróżnicowanych produktów. Powszechny dostęp do informacji poprzez Internet i media telewizyjne sprawia, że konsumenci dokonują wyboru spośród nieograniczonej...
Producenci w wielu branżach, coraz częściej podążając za potrzebą klienta, sukcesywnie zwiększają wachlarz oferowanych wyrobów. W niektórych gałęziach przemysłu klienci mają możliwość współuczestnictwa w procesie konstruowania wyrobu, który później wytwarzany jest przy uwzględnieniu konkretnych wymagań postawionych przez klienta. Z drugiej strony duża konkurencja wymusza na producentach zagwarantowanie niskich cen tego rodzaju usług. Doprowadziło to do powstania nowej koncepcji zarządzania nazwanej „Mass Customization”. Jednym z podstawowych wyznaczników tej koncepcji jest zagwarantowanie stosunkowo niskich cen za wysoko zindywidualizowane wyroby dostarczane w stosunkowo krótkim czasie.
Maksymalizacja zdolności
Ażeby zagwarantować niską cenę zakupu, koniecznym staje się utrzymanie niskich kosztów wytwarzania. Jednym z najważniejszych warunków, które muszą zostać spełnione, aby zapewnić niskie koszty produkcji, jest maksymalizacja wykorzystania istniejących zdolności produkcyjnych. Jest to zagadnienie złożone i skomplikowane z dwóch powodów. Po pierwsze, w warunkach „Mass Customization” produkcja wyrobu finalnego jest uruchamiana bezpośrednio na zamówienie klienta. W wyniku zmienności w popycie zamówienia te spływają z różną intensywnością. Zmienność taka wyraża się w zróżnicowanej liczbie zamówień składanych w poszczególnych okresach planistycznych. W dłuższym okresie w skali roku występują dodatkowe wahania sezonowe, które nakładając się z „normalnymi” wahaniami, niosą ze sobą istotne różnice w zapotrzebowaniu na produkowane wyroby w analogicznych okresach.
W warunkach „Mass Customization” produkcja wyrobu finalnego jest uruchamiana bezpośrednio na zamówienie klienta
Po drugie, w skład szerokiego asortymentu produktów wchodzą wyroby o różnym poziomie pracochłonności. W praktyce oznacza to, że jeden wyrób jest mniej złożony i produkuje się go szybciej niż wyrób inny, o wyższym poziomie złożoności. Zdarzyć się może sytuacja, że w danym okresie klienci zamówili produkty o mniejszej pracochłonności, przez co nastąpi niepełne wykorzystanie zdolności produkcyjnych. Z kolei w przypadku odwrotnym, kiedy wystąpi zapotrzebowanie na bardziej złożone produkty, zdolności produkcyjne mogą okazać się niewystarczające. Dlatego też zachodzi konieczność zastosowania metod pozwalających na maksymalizację wykorzystania zdolności produkcyjnych w warunkach produkcji o szerokim wachlarzu asortymentu, uruchamianej bezpośrednio dla klienta. Poniżej zestawione zostały najważniejsze metody i praktyki zebrane na podstawie obserwacji działań gospodarczych (trzy firmy zajmujące się produkcją stolarki okiennej oraz producent układów elektronicznych, a także producent dekoracji okiennych).
Mass Customization
Uwarunkowania wynikające z Mass Customization, w których chodzi o szerokie zabezpieczanie zindywidualizowanych potrzeb klienta, tworzą pewien konflikt z interesami producentów dysponujących zdolnościami produkcyjnymi. W interesie tych drugich jest zapewnienie w miarę stałego i pełnego obciążenia istniejących zdolności wytwórczych, a zwłaszcza obciążenia dla zatrudnianych pracowników, np. w sytuacji gdy produkcja wyrobów odbywa się „na magazyn”. W praktyce Mass Customization produkcja na magazyn stanowi tylko nieznaczny udział w stosunku do całości produkcji i dlatego też to producent musi dostosowywać zdolności produkcyjne do aktualnego portfela złożonych zamówień.
W praktyce Mass Customization produkcja na magazyn stanowi tylko nieznaczny udział w stosunku do całości produkcji
Ogólnie metody zarządzania zdolnością produkcyjną można podzielić na takie, które zapewniają utrzymanie zdolności produkcyjnych na stałym poziomie oraz takie, które w pewnym zakresie dostosowują na bieżąco zdolności produkcyjne do aktualnych potrzeb wynikających ze złożonych zamówień klientów (Tab1).
Metody stabilizujące zdolność produkcyjną
Produkt uniwersalny
Metoda ta polega na znalezieniu w swoim portfelu kilku produktów, które klienci wybierają najczęściej i produkowaniu ich w systemie na magazyn. W takim rozwiązaniu hybrydowym 80-90 proc. produktów wytwarzanych jest na zamówienie, natomiast 10-20 proc. produktów uniwersalnych trafia do magazynu. Zapas taki absorbuje fluktuację w popycie, podobnie jak to się dzieje w przypadku klasycznej metody produkcji na magazyn – w sytuacji mniejszego zapotrzebowania na zdolności produkcyjne uwalnia się produkcję towarów uniwersalnych, a w sytuacjach przekroczenia maksymalnych zdolności produkcyjnych niedobór pokrywany jest zapasami tychże produktów uniwersalnych. Korzyścią zastosowania takiej metody jest wysoka skuteczność w stabilnym wykorzystaniu zdolności produkcyjnych, natomiast do wad zaliczyć można konieczność utrzymywania zapasów, co wiąże się z dodatkowymi kosztami. Należy też zaznaczyć, że nie wszystkie przedsiębiorstwa produkujące na zamówienie są w stanie wyznaczyć powtarzalny produkt uniwersalny. Metoda ta jest szeroko używana przez jednego z największych producentów stolarki okiennej na rynku szwedzkim.
Zmienny czas dostawy do klienta
Koncepcje zmiennego czasu dostawy do klienta nazwać można kolejkowaniem zamówień na wejściu procesu produkcyjnego. Przy wzroście popytu kolejka ta się wydłuża, a tym samym rośnie czas dostawy do klienta. Kolejka zostaje „rozładowana” w okresach mniejszego zapotrzebowania na zdolność produkcyjną. Mimo że rozwiązanie takie może wiązać się z utratą potencjalnych klientów, jest szeroko stosowane w wielu gałęziach przemysłu. Dobrym przykładem jest przemysł motoryzacyjny, w którym wzrost popularności na konkretny model może skutkować wydłużeniem czasu oczekiwania nawet do sześciu miesięcy. W przypadku sytuacji odwrotnej, gdy występuje nadwyżka zdolności produkcyjnej, uwalniane są zamówienia z dłuższym czasem realizacji i w zależności od podpisanych umów sprzedażowych dostarcza się je wcześniej do klienta bądź magazynuje na koszt własny. Sytuacja taka ma miejsce w badanych przedsiębiorstwach stolarki budowlanej, w których w razie potrzeby uwalnia się na produkcję zamówienia na realizacje projektów budowlanych oddalonych w czasie. Wadą tego rozwiązania jest konieczność magazynowania tychże produktów na koszt własny.
Dywersyfikacja w końcowej fazie produkcji
Korzystnym rozwiązaniem gwarantującym większą stabilność wykorzystania zdolności produkcyjnej jest przeniesienie „punktu zróżnicowania” wyrobów na koniec procesu produkcyjnego. Taka metoda zastosowana została u jednego z producentów żaluzji i rolet okiennych, gdzie cały asortyment począwszy od tkanin, a skończywszy na metalowych detalach wykończeniowych wytwarzany jest na magazyn, który w tej sytuacji jest zapasem absorbującym fluktuacje w zapotrzebowaniu na zdolność produkcyjną. Dopiero proces montażu finalnego działa w oparciu o konkretne zlecenia klientów. Zaletą tej metody jest możliwość zastosowania klasycznej produkcji na magazyn, natomiast istotną wadą są ograniczenia w jej zastosowaniu, gdyż w wielu gałęziach przemysłu ograniczenia technologiczne nie pozwalają na taką organizację produkcji.
Outsourcing
Praktyka outsourcingu polega na wykorzystaniu zdolności produkcyjnych swojego podwykonawcy i może również skutecznie wspomagać zarządzanie zdolnością produkcyjną. W przypadku wystąpienia większego zapotrzebowania na zdolność produkcyjną nadwyżkę produkcji zleca się partnerowi biznesowemu.
Metoda ta została zaobserwowana w badanym przedsiębiorstwie produkującym układy elektroniczne. W przypadku stabilnego popytu podwykonawca otrzymywał jedynie niewielkie zamówienia, które miały zapewnić utrzymanie niezbędnej wiedzy technologicznej. W okresach większego zapotrzebowania nadwyżka produktów w całości trafiała do podwykonawcy. Największą wadą tego rozwiązania jest konieczność transferu wiedzy dotyczącej technologii wytwarzania, która w niektórych branżach jest elementem przewagi konkurencyjnej.
Aby zapewnić niskie koszty produkcji konieczna jest maksymalizacja wykorzystania istniejących zdolności produkcyjnych
Innym niekorzystnym aspektem jest fakt, że metoda ta polega na przeniesieniu fluktuacji wykorzystania zdolności produkcyjnej na podwykonawcę, który może wliczyć związany z tym spadek skuteczności w cenę usługi.
Metody dopasowujące zdolność produkcyjną
Godziny nadliczbowe
Jest to najprostszy i najszybszy sposób reagowania na zmienność w popycie. W przypadku zwiększonego zapotrzebowania planuje się dodatkowe godziny pracy, często w godzinach nocnych. Niestety jest to rozwiązanie kosztowne, ponieważ koszt godziny nadliczbowej jest wyższy niż godziny nominalnej. Dodatkowo godziny nadliczbowe mogą pokryć jedynie niewielkie fluktuacje (tylko w przypadku braku zdolności produkcyjnej), więc nie nadają się do zastosowania w przypadku dużych wahań sezonowych.
Kolejnym czynnikiem ograniczającym stosowanie tej metody jest konieczność utrzymywania w trakcie doby wolnej rezerwy czasowej, co jest niemożliwe w przypadku trzyzmianowego systemu pracy. Niemniej z racji łatwości zastosowania metoda ta jest używana we wszystkich opisywanych przedsiębiorstwach.
Długi okres rozliczeniowy
Polski kodeks pracy umożliwia wprowadzenie dłuższego niż miesiąc okresu rozliczeniowego, w ramach którego w sposób elastyczny planować można czas pracy. Stosując taki okres, pracodawca nie jest związany wymiarami czasu pracy w poszczególnych miesiącach, lecz wymiarem obowiązującym w całym tym okresie.
Takie rozwiązanie umożliwia skrócenie czasu pracy w okresie o niskim zapotrzebowaniu i proporcjonalne wydłużenie czasu pracy, kiedy następuje konieczność zwiększenia zdolności produkcyjnej. W praktyce w jednym miesiącu można na przykład zaplanować 4-dniowy tydzień pracy, a w kolejnym dokonać wyrównania czasu pracy poprzez zaplanowanie 6-dniowego tygodnia pracy. Istotną wadą tego rozwiązania jest ograniczony okres, w którym można dokonywać zmian w czasie pracy. W roku 2012 maksymalny okres rozliczeniowy zdefiniowany przez ustawodawcę to 4 miesiące.
Pracownicy tymczasowi
Popularną ostatnio metodą kompensacji fluktuacji w zapotrzebowaniu na zdolność produkcyjną stało się wykorzystanie pracowników tymczasowych, zatrudnionych poprzez agencje pracy tymczasowej. Rozwiązanie to przynosi wiele korzyści pracodawcy – szybką dostępność pracowników, zredukowaną liczbę czynności administracyjnych związanych z zatrudnianiem czy też możliwość natychmiastowej redukcji zdolności produkcyjnej.
Pośrednictwo takie posiada również istotną wadę – wyższy koszt pracy, co wiąże się z kosztem pośrednictwa przez agencje pracy. Inną, mniej policzalną wadą jest niższa zazwyczaj motywacja pracowników tymczasowych, którzy nie mają poczucia stabilności zatrudnienia i nie w pełni identyfikują się przedsiębiorstwem, któremu pośrednio świadczą pracę. Rozwiązanie to zastosowane było w dwóch opisywanych przedsiębiorstwach, jednakże z racji wyżej wymienionych wad firmy były w trakcie odstępowania od tej koncepcji.
Zmienny poziom zatrudnienia
Innym popularnym rozwiązaniem stosowanym przez przedsiębiorstwa jest dynamiczne dopasowanie poziomu zatrudnienia do realiów rynkowych. W konsekwencji konieczne są okresowe zwolnienia i ponowne zatrudnianie.
Polski kodeks pracy, zwłaszcza w porównaniu z przepisami z innych krajów Europy Zachodniej, daje możliwość stosunkowo łatwego rozwiązania umowy o pracę. Dla przykładu umowa o pracę na czas określony może zostać rozwiązana z dwutygodniowym okresem wypowiedzenia bez podania przyczyny rozwiązania umowy. Metoda ta mimo swej pozornej prostoty jest obarczona wieloma wadami.
Proces zwalniania i ponownej rekrutacji wiąże się z kosztami, które są trudno mierzalne. Do najważniejszych zaliczyć należy koszty ponownego szkolenia, koszty znalezienia nowych pracowników czy też koszty ewentualnych odpraw pracowniczych. Innym niepożądanym efektem jest utrata stabilności zatrudnienia oraz spadek motywacji pracowników. W przypadku większej redukcji pracowników koniecznym staje się uruchomienie procesu zwolnień grupowych, który psuje wizerunek marki na lokalnym rynku pracy.
Realokacja zasobów produkcyjnych
Często w przedsiębiorstwach oferujących wysoki wachlarz asortymentu są wydzielone linie technologiczne czy też oddzielne zakłady specjalizujące się w poszczególnych grupach produktów. W takim przypadku zwiększenie elastyczności zdolności produkcyjnej uzyskać można dwojako.
Pierwszy sposób polega na możliwości wytwarzania grup produktowych na kilku liniach lub w kilku zakładach produkcyjnych. W takim przypadku mniejsze zapotrzebowanie na zdolność jednej linii produkcyjnej może zostać wykorzystane przez inną grupę produktów, która w danym okresie wymaga większych zdolności produkcyjnych. Warunkiem koniecznym takiego rozwiązania jest zapewnienie możliwości technologicznych produkcji wielu grup produktowych, co często okazuje się bardzo kosztowne, albo nawet niemożliwe.
Drugim sposobem jest realokacja pracowników pomiędzy liniami/zakładami. Analogicznie spadek popytu na daną grupę produktową uwalnia część zasobów ludzkich, które mogą być wykorzystane na innej linii bądź w innym zakładzie produkcyjnym. W tym przypadku zasadniczym aspektem związanym z użyciem tej metody jest konieczność zapewnienia szkoleń dla pracowników z obsługi większej liczby maszyn i urządzeń. Metoda ta stosowana jest z powodzeniem w wyżej wymienionych przedsiębiorstwach.
Powiązanie metod
Produkcja wyrobów w warunkach „Mass Customisation” charakteryzuje się dużą zmiennością zapotrzebowania na zdolności produkcyjne. W przeciwieństwie do klasycznej metody produkcji masowej na magazyn często brak jest możliwości użycia zapasu produktów gotowych do kompensacji zmienności w popycie. Żadna z wyżej wymienionych metod nie jest pozbawiona wad, jednakże z obserwacji przedsiębiorstw wynika, że zastosowanie kombinacji tych metod zapewnia racjonalne wykorzystanie istniejących zdolności produkcyjnych, tj. zapewnia wysoką ich elastyczność a jednocześnie minimalizuje negatywny wpływ zmiennego zapotrzebowania na zdolności produkcyjne na zatrudnionych pracowników i zapewnia utrzymanie kosztów wytwarzania na poziomie porównywalnym z produkcją masową.