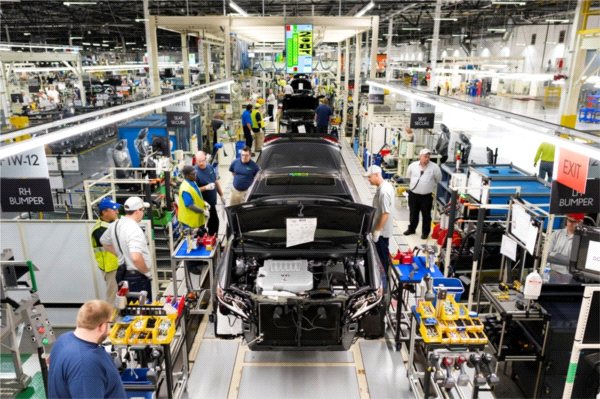
TPS XXI wieku
System Produkcyjny Toyoty (Toyota Production System - TPS) stoi u podstaw większości nowoczesnych metod zarządzania produkcją. TPS ma już ponad 50 lat, ale wciąż z powodzeniem funkcjonuje w fabrykach. Zmiany związane z czwartą rewolucją przemysłową sprawiają jednak, że TPS musi...
Toyota swoją nową filozofię produkcji samochodów nazwała Toyota New Global Architecture (TNGA) i jest aktualne na etapie jej wdrażania. Łatwo zauważyć, że w znacznym stopniu adaptuje ona założenia czwartej rewolucji przemysłowej. System Produkcyjny Toyoty pozostaje jednak fundamentem działalności koncernu.
Niespotykana elastyczność
Toyota jest znana na całym świecie ze swojego TPS, który wykładany jest na uczelniach i który uratował przed poważnymi kłopotami lub nawet bankructwem już niejedną firmę. Większość producentów samochodów w taki czy inny sposób zaadaptowało sposoby organizacji produkcji, projektowania i zarządzania wypracowane przez Toyotę. Zgodnie z zasadą Kaizen japońska firma metodą drobnych kroków stale udoskonala te procesy.
Pomimo tych sukcesów, potwierdzonych pozycją największego producenta samochodów na świecie, kilka lat temu japońska firma zdecydowała się na przeorganizowanie swojego Systemu Produkcji całkowicie od podstaw. Intensywne planowanie trwało 3 lata i na początku 2015 roku prezes koncernu Akio Toyoda ogłosił rozpoczęcie wdrażania nowej architektury i organizacji produkcji o nazwie Toyota New Global Architecture (TNGA). Zmiany dotyczą w zasadzie wszystkich płaszczyzn działania firmy – od procesu projektowania aut przez konstruowanie linii produkcyjnych i fabryk po globalne podejście do części i podzespołów w taki sposób, żeby poszczególne elementy były jak najbardziej uniwersalne i pasowały do maksymalnie wielu modeli. Nowe podejście zakłada niespotykany dotąd stopień elastyczności i uniwersalności,. Przyjrzyjmy się temu, jak będą wyglądały przyszłe fabryki Toyoty.
Fabryki nowej generacji
Tradycyjne fabryki to wielkie struktury pełne ciężkiego sprzętu. Są drogie w budowie i utrzymaniu, dlatego aby ich praca była opłacalna, trzeba stale wykorzystywać co najmniej 75 proc. ich możliwości produkcji. Maszyny są zazwyczaj na tyle drogie, że muszą pracować przez co najmniej 10 lat, aby inwestycja w nie się zwróciła.
Fabryki nowej generacji zaprojektowane według nowej architektury Toyoty to proste, stosunkowo niewielkie, jednokondygnacyjne konstrukcje. Będą tańsze w budowie i w utrzymaniu, m.in. dzięki zużyciu mniejszej ilości prądu, wody i ciepła niż tradycyjne fabryki. Sprzęt na liniach produkcyjnych będzie kompaktowy i niewysoki, dzięki temu będzie można w większym stopniu korzystać z naturalnego światła.
Modułowe maszyny i linie produkcyjne
Bazując na najważniejszych osiągnięciach swojego słynnego Systemu Produkcji, Toyota opracowała od nowa konstrukcje linii produkcyjnych. Ich modułowa struktura pozwoli szybciej dostosowywać je do zmieniających się modeli oraz łatwiej wprowadzać nowe technologie. Przenośnik taśmowy będzie umocowany bezpośrednio na podłodze i podzielony na segmenty. Można będzie go dowolnie wydłużać lub skracać, po prostu dodając lub odłączając modułowe fragmenty.
Linie produkcyjne o elastycznej długości służą temu, aby można było łatwo dokładać lub odejmować maszyny produkcyjne. Sprzęt nowej generacji będzie poruszał się na rolkach, nie będzie mocowany na stałe do podłogi. Taka elastyczność pozwoli na częste aktualizowanie wersji modeli i dodawanie nowych elementów wyposażenia.
Nowe technologie produkcji
Toyota wprowadziła nowy pomysł na linie lakiernicze. Współczesne lakiernie o przepustowości 50 tys. samochodów rocznie to ogromne budowle o 10 m wysokości i 187 m długości. Toyota zmniejszyła lakiernię do 6,5 m wysokości i 149 m długości, a dodatkowo wyposażyła ją w system wychwytywania i zbierania rozpryskującego się w powietrzu lakieru. Nowa lakiernia będzie dzięki temu czystsza, oszczędniejsza i bardziej ekologiczna.
Technika laserowa zastąpi tradycyjne spawanie, przynosząc ogromną oszczędność czasu. Wykonanie jednego spawu standardową metodą trwa 2-2,5 s, natomiast spaw laserowy zajmuje tylko od 0,3 do 1 s. Laser zapewnia dużo większą wytrzymałość spoin i może obrabiać zarówno stal, jak i aluminium.
Deski rozdzielcze produkowane metodą wylewania mają najwyższą jakość, jednak są drogie w produkcji. Inżynierowie opracowali nową prostą maszynę odlewniczą, która jest o 60% mniejsza, zużywa o 30% mniej energii i obniża koszty o 20 proc..
Nowa maszyna odlewnicza wykorzystywana w produkcji zderzaków pozwala na tak szybkie przezbrojenie, że zderzaki mogą być wytwarzane w krótkich seriach, tuż pod otrzymaniu zamówienia z montowni danego modelu. Dzięki temu fabryki będą wykorzystywały mniejszą przestrzeń magazynową.
Podejście proekologiczne
W ramach TNGA funkcjonować będą też liczne innowacje ekologiczne. Toyota opracowała nowy system chemicznego magazynowania energii termicznej, oparty na związkach magnezu, który odzyskuje i przechowuje tracone ciepło. To pozwoli obniżyć emisję dwutlenku węgla ze spalanego gazu o 15 proc..
Panele fotowoltaiczne zamontowane w fabrykach będą służyły zarówno do wytwarzania energii elektrycznej, jak i do podgrzewania wody. To znacząco obniży zapotrzebowanie fabryk na prąd z zewnętrznych źródeł i zmniejszy ich wpływ na środowisko.
Toyota prowadzi ponadto dwutorową politykę względem zużytych baterii hybrydowych. Akumulatory zbyt słabe, by pracować w samochodzie, mają jeszcze wystarczającą pojemność, żeby służyć do magazynowania energii ze źródeł odnawialnych. Dopiero całkowicie wyeksploatowane ogniwa firma poddaje recyclingowi. Takie magazyny energii służą już m.in. w Parku Narodowym Yellowstone, a teraz znajdą także zastosowanie w nowych fabrykach koncernu.
Grupowanie bliźniaczych modeli
Toyota zamierza przenosić produkcję modeli w taki sposób, aby zgrupować podobne auta w tych samych fabrykach. Dzięki temu zwiększa się uniwersalność modułowych linii produkcyjnych i upraszcza logistyka. Wskaźnik średniego wykorzystania linii produkcyjnej w koncernie wzrósł z 70 proc. w 2009 roku do ponad 90 proc. obecnie. Różne modele podobnej wielkości będą dzieliły wspólne platformy i komponenty, co skróci czas projektowania nowych modeli i zmniejszy jego koszty o co najmniej 20 proc..
Elastyczność i kastomizacja
Wdrożenie TNGA sprawi, że budowa fabryk i przygotowywanie linii produkcyjnych będzie szybsze i tańsze, zarządzanie częściami będzie prostsze i pozwoli uwolnić przestrzeń magazynową, a samochody będą powstawały szybciej, zarówno na etapie projektowania, jak i na taśmie produkcyjnej. To pozwoli nie tylko na częstsze odświeżanie modeli i wprowadzanie nowych generacji, ale nawet umożliwi realizowanie zamówień klientów dotyczących wersji wyposażenia od razu na taśmie produkcyjnej czy ułatwi produkcję edycji specjalnych.
Obecnie znamy 2 modele zbudowane według nowej koncepcji – są to Prius oraz hybrydowy crossover C-HR. W ciągu kilku lat Toyota zamierza wprowadzić TNGA do połowy swoich modeli na całym świecie.
Projektowanie z myślą o TNGA
Zmiana metod produkcji wpłynie także na proces projektowania samochodów. Procesy projektowania i produkcji samochodów zostaną uproszczone przede wszystkim poprzez standaryzację wymiarów i położenia zasadniczych podzespołów w obrębie ujednoliconych platform nowych pojazdów.
Zastosowanie takich samych podzespołów w różnych modelach należących do różnych segmentów ograniczy liczbę części, które trzeba zaprojektować, następnie wytwarzać za pomocą różnych urządzeń, na koniec zaś osobno dostarczać. Toyota ocenia, że TNGA zmniejszy pracochłonność projektowania pojazdów o 20 proc.